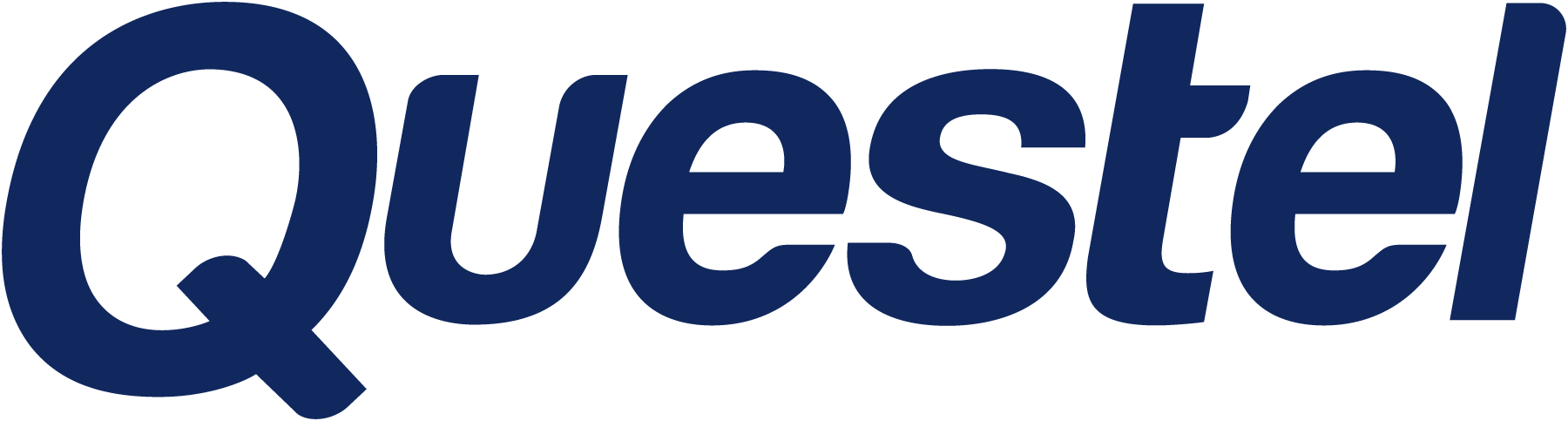
- Patent
- Our Patent solutions
- IP Intelligence SoftwareStreamline the journey from innovation to IP with our IP intelligence software, patent search, data analytics, and related services and tools.→ Read moreOur solutionsPowerful patent searching and analysisArtificial intelligence for patent classificationGrant statistics and detailed legal status analysisSmall molecules searching and analysisDNA and amino acid searching and analysisExplore new markets and opportunitiesEasy patent searching and collaborationAnalysis from any scientific sourcesUnlock AI-powered use cases across a range of Questel software.SEP DatabaseNEWStandard Essential Patent Data & AnalyticsLatest resources
- → Smart Patent Research for True IP ProfessionalsThe value of a patent search hinges on two key factors: data quality and the intelli...
- → A Guide to Bio Sequence Patent SearchingBio sequence patent search is a unique type of life-science search requiring special...
- → The World’s Leading 5G SEP Owners – 2025Explore the 2025 rankings of the top 5G SEP owners in our latest report. Learn how g...
- → Smart Patent Research for True IP Professionals
- IP Management SoftwareKeep your assets up to date and aligned with your corporate strategy with our Equinox suite of IP management software, data analytics, and eBilling tools→ Read moreOur solutionsPowerful all-in-one IPMS for corporatesIPMS tailored for large corporates, built on SalesforcePowerful all-in-one IPMS for law firmsIPMS tailored for large Law FirmsCollaborative invention-to-filing workflowLatest resources
- → Equinox Corporate+ – Leveraging Salesforce for Large IP Portfolio OwnersIP management is evolving fast to keep up with a rapidly changing landscape. In this...
- → Transform How You Manage Your IP Portfolio with Equinox IP Management Software By integrating data, services, and artificial intelligence (AI) capabilities, modern...
- → A Goal to Boost Efficiency by 30%: Why Brandstock Chose Equinox Law Firm Driven by its goal to deliver the “best IP service to clients,” leading law firm Bra...
- → Equinox Corporate+ – Leveraging Salesforce for Large IP Portfolio Owners
- Preparation & Prosecution CopilotsOptimize your entire patent process with our range of advanced Preparation & Prosecution Copilots, from patent application drafting to prosecution workflow automation, claims mapping, and office action responses.→ Read moreOur solutionsAll-in-one patent prosecution workflow, data, and collaboration workspace.AI-DraftingNEWIndustry-leading patent drafting software powered by generative AI.Patent Mapping and Claim Analysis with AIPatent Office Action Response Management with AILeverage the power of data to guide your patent prosecution with Prosecution PackLatest resources
- → 5 Challenges for IP Professionals in the Next 5 Years—and How to Overcome ThemArtificial intelligence (AI) is a hot topic in the IP sector due to its potential to...
- → Pathways to Productivity: What our 2025 Industry Outlook Research Reveals About AI in IPDiscover what our 2025 Industry Outlook Research reveals about AI adoption by the IP...
- → 3 Cutting-Edge Solutions to Support Your R&D and Innovation Strategies Discover how the latest cutting-edge software and AI-elevated processes for research...
- → 5 Challenges for IP Professionals in the Next 5 Years—and How to Overcome Them
- Patent ServicesBenefit from end-to-end support for vital but time-consuming administrative tasks with our complete range of patent support services, including searches, translations, international filings, validations, unitary patent management, recordals, renewals, and more→ Read moreOur solutionsPatentability, Freedom-To-Operate, InvalidityPCT & national phase, Paris Convention, Unitary PatentUnitary Patent and Unified Patent Court servicesSimplified European validation servicesCentralized patent translation servicesFee and renewals managementAssignment and recordal of all IP RightsLatest resources
- → What You Need to Know About Maintaining Intellectual Property Records Maintaining intellectual property records can be complicated for in-house legal team...
- → Should You Outsource Intellectual Property Management Services? Whether you manage a small portfolio or multiple large ones, intellectual property m...
- → 4 Major Intellectual Property Issues in Mergers and Acquisitions Merger and acquisition (M&A) activities present many challenges to buyers and seller...
- → What You Need to Know About Maintaining Intellectual Property Records
- Patent Strategy & Administration→ Read more
Control costs, streamline invoices, and safeguard your patent rights efficiently with our patent strategy & administration services and tools
Our solutionsEnd-to-end IP admin, data verification and docketingInvoice review, bundling and paymentFee audits, negotiation, compliance, benchmarks and forecastingLandscaping, benchmarking, valuation and licensingDefensive PublicationBUY ONLINEPublish an invention into the public domainLatest resources- → 4 Good Reasons to Outsource Trademark DocketingTrademark docketing requires time, effort, and resources, placing a strain on many b...
- → Should You Outsource Intellectual Property Management Services? Whether you manage a small portfolio or multiple large ones, intellectual property m...
- → 3 Cutting-Edge Solutions to Support Your R&D and Innovation Strategies Discover how the latest cutting-edge software and AI-elevated processes for research...
- → 4 Good Reasons to Outsource Trademark Docketing
- TrademarkNew
- Our Trademark solutions
- Clearance & Watch PlatformScreen and monitor your brand and trademark rights effectively with our trademark clearance search and trademark monitoring platform→ Read moreOur solutionsScreen trademarks with AI-driven search technologyMarkify Comprehensive SearchBUY ONLINEAI-driven trademark availability softwareBest-in-class trademark results paired with key pharmaceutical sourcesWatch for new, identical and confusingly similar trademarksMonitor marketplaces, social media, and web contentLatest resources
- → From Detection to Defense: A Powerful Duo that Tackles Trademark Proof of Use Could your or your competitors’ rights be vulnerable to revocation based on non-use ...
- → Artificial Intelligence and IP: What’s on the Horizon for AI and Trademarks? Discover what’s on the horizon for artificial intelligence and IP, including powerfu...
- → Crossing the Frontier with AI Trademark Search: Where Algorithms Intersect with Human Expertise From manual analysis to AI trademark search, discover how combining AI algorithms wi...
- → From Detection to Defense: A Powerful Duo that Tackles Trademark Proof of Use
- IP Management SoftwareManage and maintain your trademark, design and domain name rights effectively with our state-of-the-art trademark management software→ Read moreOur solutionsPowerful all-in-one IPMS for corporatesIPMS tailored for large corporates, built on SalesforcePowerful all-in-one IPMS for law firmsIPMS tailored for large law firmsCollaborative worklfow for trademark and design proposalsLatest resources
- → Equinox Corporate+ – Leveraging Salesforce for Large IP Portfolio OwnersIP management is evolving fast to keep up with a rapidly changing landscape. In this...
- → 4 Good Reasons to Outsource Trademark DocketingTrademark docketing requires time, effort, and resources, placing a strain on many b...
- → Transform How You Manage Your IP Portfolio with Equinox IP Management Software By integrating data, services, and artificial intelligence (AI) capabilities, modern...
- → Equinox Corporate+ – Leveraging Salesforce for Large IP Portfolio Owners
- AI Assistants for Trademark ProductivityReview trademark search and watch results, create first drafts of goods and services descriptions, classify evidence of use, and manage office action responses effectively with our AI assistants for trademark productivity.→ Read moreOur solutionsAll-in-one digital trademark workflow automationChat with trademark search or watch results to review findings and assess riskSave time and build consistency and compliance with our AI solutionAnalyze content and draft answers with AIManage trademark evidence of use with AILatest resources
- → 5 Challenges for IP Professionals in the Next 5 Years—and How to Overcome ThemArtificial intelligence (AI) is a hot topic in the IP sector due to its potential to...
- → From Detection to Defense: A Powerful Duo that Tackles Trademark Proof of Use Could your or your competitors’ rights be vulnerable to revocation based on non-use ...
- → Experience AI Copilots in Action: The All-in-One IP Solution That Supercharges Patent & Trademark ProductivityTo stay innovative when developing new products and processes in a fast paced enviro...
- → 5 Challenges for IP Professionals in the Next 5 Years—and How to Overcome Them
- Trademark, Design & Domain Services→ Read more
Access expert support throughout the complete brand lifecycle with our integrated domain name, design, and trademark solutions
Our solutionsAnalyst-driven searches with on-demand and customizable reportingIP asset monitoring with intelligent pre-selectionCase management and take-down servicesInternational registration process supportTrademark and design renewal servicesEffective management of corporate domain namesAssignment and recordal of all IP rightsEnd-to-end IP admin, data verification, docketingLatest resources- → Why Do Companies Outsource IP Tasks? Because They Want to Reach Their KPIs! While normally associated with internal metrics, key performance indicators (KPIs) c...
- → What You Need to Know About Maintaining Intellectual Property Records Maintaining intellectual property records can be complicated for in-house legal team...
- → Trademark and Brand Protection Hot Topics: a discussion about trends and news from IACC & INTAOur teams attended INTA and IACC, key events in the intellectual property world. The...
- → Why Do Companies Outsource IP Tasks? Because They Want to Reach Their KPIs!
- Innovation
- Our Innovation solutions
- Innovation Management SoftwareMake your innovation management processes faster, efficient and scalable with our end-to-end innosabi innovation management platform.→ Read moreOur solutionsBusiness-oriented dashboards for innovatorsStartup deal flow and program managementCollaborative idea and innovation managementCustomers co-creation and communitiesPartners co-innovation and open callsInnovation Project ManagementUnlock AI-powered use cases across a range of Questel software.Latest resources
- → 5 Reasons to Invest in Innovation Management SoftwareTranslating innovative ideas into successful products is becoming increasingly compl...
- → 9 Ways to Build a Successful Innovation Culture To embed innovation fully into their organizations, companies are often told they ne...
- → 3 Cutting-Edge Solutions to Support Your R&D and Innovation Strategies Discover how the latest cutting-edge software and AI-elevated processes for research...
- → 5 Reasons to Invest in Innovation Management Software
- Innovation ServicesSuccessful innovation processes and culture are about more than the right software tools. Our innovation services leverage proven methods and approaches to generate insights, ideas, and solutions.→ Read moreOur solutionsMarket screening, Competitive intelligence and Technology scoutingConnect with partners, improve or localize your innovation processProducts and services namingSeamless user experience to a global audienceEngage with new audience globallyLatest resources
- → 7 Key Questions to Measure Innovation Management Success Innovation is the key to staying competitive in today’s fast-paced business world. H...
- → Software Patent: How Can It Be Done?Even though life without computers is today nearly impossible to imagine, patent-bas...
- → What is Innovation Scouting?Change is a constant. New technologies surface regularly and change existing product...
- → 7 Key Questions to Measure Innovation Management Success
- SolutionsAI
- Solutions
- Artificial Intelligence in IP→ Read more
Discover Questel’s holistic and responsible approach to artificial intelligence
and intellectual property and our vision to inspire the future of IP with AIOur solutionsDiscover how AI is transforming IPIndustry-leading patent drafting software powered by generative AIAI copilots for optimized patent preparation and prosecution workflowsAI copilot for automated patent classificationAI copilot for elevated trademark clearance searchUnlock AI-powered use cases across a range of Questel software.Proof of UseNewCapture Trademark Evidence of Use with AILatest resources- → The Future of IP Departments: Are We Headed Toward a World of Only Chatbots and AI?In this on-demand session, industry leaders from Questel and Better Ipsum discuss ho...
- → Pathways to Productivity: What our 2025 Industry Outlook Research Reveals About AI in IPDiscover what our 2025 Industry Outlook Research reveals about AI adoption by the IP...
- → Leverage Artificial Intelligence to Simplify Your Prosecution WorkUnlock exclusive insights and discover how Qthena, the AI-powered prosecution assist...
- → The Future of IP Departments: Are We Headed Toward a World of Only Chatbots and AI?
- Integrated IP Ecosystem→ Read more
Optimize your intellectual property assets with our comprehensive IP portfolio management solutions,
ensuring maximum protection and strategic advantage for your business.Our solutionsIP management systems, docketing, forecasting, data analytics, blockchain, and eBilling toolsOur web-based platform for IP services managementPAVIS Connect, our solution for companies and laws firms that already have an IP management systemAccess trademark watches directly from Equinox with Markify Watch integrationLatest resources- → Switching to a New IPMS: What Does the Data Migration Process Involve?When you’re considering switching to a new IP management system (IPMS), you’ll likel...
- → When Is the Right Time to Upgrade Your IP Management Software?When you are overloaded by IP administrative tasks and deadlines, switching to a new...
- → The Power of IPMS Technology for IP Lifecycle Management By choosing an end-to-end integrated IP management system (IPMS), you can build effi...
- → Switching to a New IPMS: What Does the Data Migration Process Involve?
- Solutions for Law FirmsStreamline internal processes, satisfy client demand, and remain competitive with our specialist solutions for law firms→ Read moreOur solutionsAll-in-one patent prosecution workflow, data, and collaboration workspace.Patent Office Action Response Management with AIIndustry-leading patent drafting software powered by generative AIPowerful all-in-one IPMS for law firmsPowerful patent searching and analysisScreen and monitor your trademark rights effectively with our Markify platformStreamline multilingual matters with fast and reliable legal translation servicesCentralized patent translation servicesFee and renewals managementTrademark and design renewal servicesLatest resources
- → How Equinox Law Firm Supports Redchip Lawyers to Save Time and Build RelationshipsFor law firms with large, multi-disciplinary practices, an IP management system (IPM...
- → Can Your IPMS Help Build Strong Client Relationships?Cultivating strong client relationships is incredibly important for IP law firms. Yo...
- → Leverage Artificial Intelligence to Simplify Your Prosecution WorkUnlock exclusive insights and discover how Qthena, the AI-powered prosecution assist...
- → How Equinox Law Firm Supports Redchip Lawyers to Save Time and Build Relationships
- Solutions for Life Sciences→ Read more
Intellectual property management tools, services, and insights to support life sciences innovation strategies
Our solutionsDNA and amino acid searching and analysisSmall molecules searching and analysisExplore new markets and opportunitiesBest-in-class trademark results paired with key pharmaceutical sourcesPowerful all-in-one IPMS for corporatesTranslation solutions across the product lifecycle—from patent to post-marketCentralized patent translation servicesFee and renewals managementTrademark and design renewal servicesLSPN North America Awards recognize QuestelLatest resources- → Patent Data Analytics, It’s Not Just for Patent SearchingThere are many reasons why organizations may conduct patent searching exercises and—...
- → Harnessing the Power of Patent AnalyticsPatent analytics can reveal new application areas, diversification opportunities, an...
- → The Technology Landscape of Precision Medicine: An IP AnalysisTechnological developments in gene sequencing, imagery, and data analysis are enabli...
- → Patent Data Analytics, It’s Not Just for Patent Searching
- Solutions for R&D and Innovation→ Read more
Strengthen, structure, and maximize your R&D and innovation strategy, workflows, and internal processes by harnessing the latest tools and technologies, including through smart application of generative AI.
Our solutionsCreate more efficient and scalable innovation management processesCollaborative invention-to-filing workflowCollaborative worklfow for trademark and design proposalsMarket screening, competitive intelligence, and technology scoutingStreamline your research and development workflows with AILatest resources- → 3 Cutting-Edge Solutions to Support Your R&D and Innovation Strategies Discover how the latest cutting-edge software and AI-elevated processes for research...
- → 7 Key Questions to Measure Innovation Management Success Innovation is the key to staying competitive in today’s fast-paced business world. H...
- → AI Patents: What Patent Mapping Can Tell Us About Future AI Technologies Artificial intelligence (AI) is evolving all the time thanks to the growing quantiti...
- → 3 Cutting-Edge Solutions to Support Your R&D and Innovation Strategies
- Language Solutions→ Read more
Translation, interpretation and tech-enabled localization services and language solutions that help global organizations open up new markets, overcome regulatory hurdles and connect with audiences worldwide.
Our solutionsStreamline multilingual matters with fast and reliable legal translation servicesTranslation solutions across the product lifecycle—from patent to post-marketManage operations, ensure compliance, and maintain consistent messaging worldwideLatest resources- → Employing A "Winning Strategy" For Your International MattersYear after year, in-house legal teams and outside counsel handling international and...
- → The Role Clinical Trial Translation Plays in Patient Recruitment and RetentionHealth equity is an essential goal in modern healthcare, and one pivotal aspect of a...
- → The difference between a legal interpreter and a legal translatorAttorneys, courts and case law often conflate the need for legal translators or lega...
- → Employing A "Winning Strategy" For Your International Matters
- Contact
- Learn & Support
- Learn and support
- Webinars & EventsAre you interested in attending one of our online or onsite event?
- Product TrainingsCustomer success is our priority. Increase your skills in the use of Questel’s software
- Product NewsA platform dedicated to software and platforms news and evolutions
- Best-in-class Customer ExperienceOur goal is to exceed our clients' expectations and share best practices
- IP TrainingIncrease the IP-IQ of your entire organization with engaging IP training programs
- Newsletter subscriptionSign up for our quarterly patent and trademark newsletters and set your email preferences below.
- Webinars & Events
- Resource HubStay up-to-date with industry best practices with our latest blogs
- Resource Hub
- About Questel
- Learn & Support
- Learn and support
- Webinars & EventsAre you interested in attending one of our online or onsite event?
- Product TrainingsCustomer success is our priority. Increase your skills in the use of Questel’s software
- Product NewsA platform dedicated to software and platforms news and evolutions
- Best-in-class Customer ExperienceOur goal is to exceed our clients' expectations and share best practices
- IP TrainingIncrease the IP-IQ of your entire organization with engaging IP training programs
- Newsletter subscriptionSign up for our quarterly patent and trademark newsletters and set your email preferences below.
- Webinars & Events
- Resource HubStay up-to-date with industry best practices with our latest blogs
- Resource Hub
- About Questel
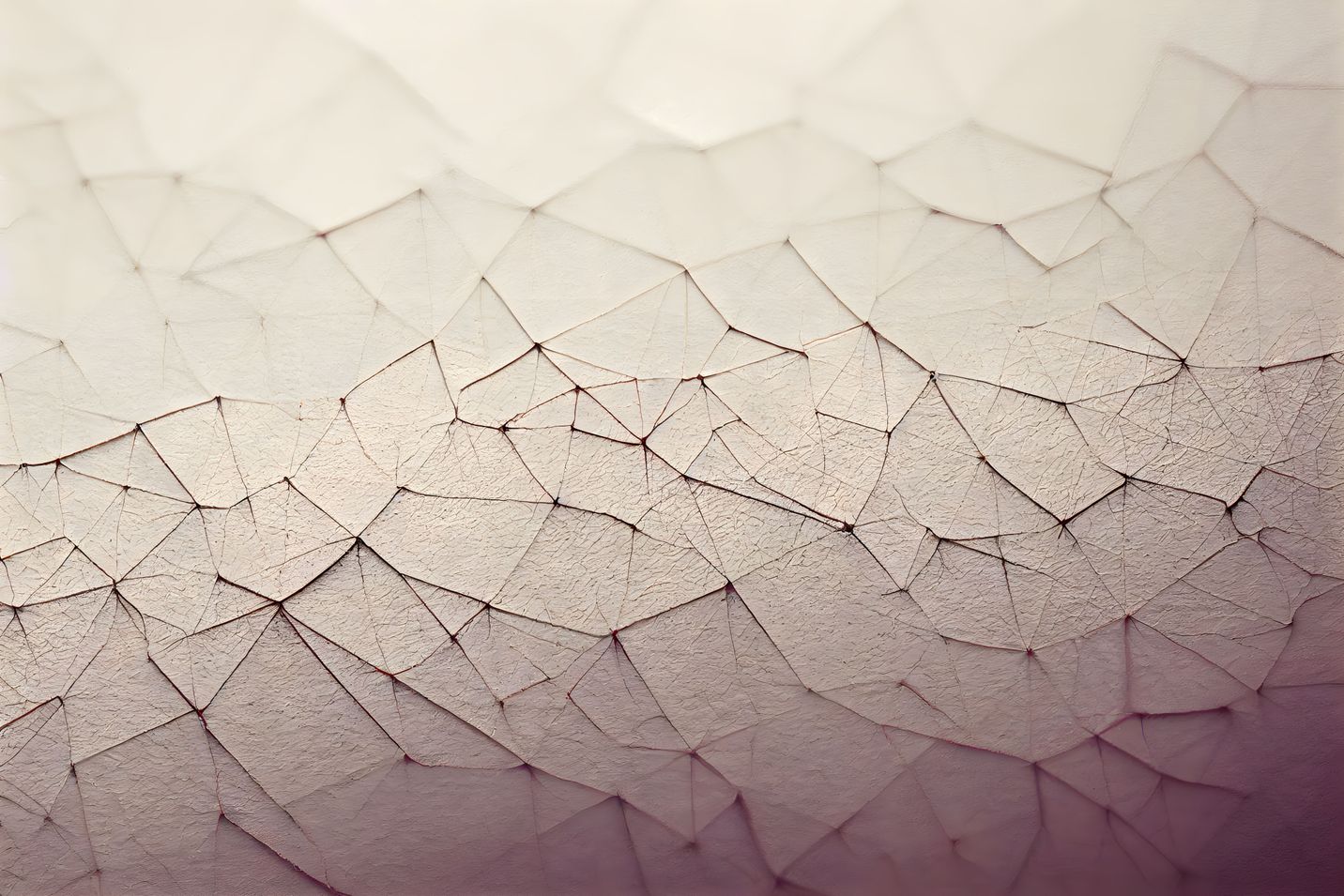
The Future of Battery Recycling: Patent Analysis of Hydrometallurgical Technology for Lithium-Ion Batteries
From electric vehicles (EVs) to renewable energy storage, lithium-ion batteries power a range of modern technologies. But what happens to the batteries when they have reached the end of their charge? Business Intelligence Consultant and Chemistry Specialist Rabeb Boughanmi shares the findings of Questel’s patent data analysis into the fast-developing field of battery recycling solutions.
Lithium-ion batteries (LIBs) power a range of modern technologies, from electric vehicles (EVs) to renewable energy storage. Among the various technologies available, LIBs stand out for their high energy density, longevity, and low self-discharge rate. The lithium-ion battery recycling market is expected to expand from US$18.58 billion in 2023 to US$31.41 billion by 2028, according to Mordor Intelligence.
The electric vehicle (EV) market is growing rapidly, driven by the need to reduce greenhouse gas emissions. By 2035, over one in four vehicles will be electric, with the EV stock growing 23% annually. This growth will lead to a significant rise in battery waste, highlighting the urgent need for effective recycling solutions to manage end-of-life batteries and reduce dependence on mining.
This focus on recycling not only addresses the demand for critical materials but also supports the transition toward more sustainable energy solutions. Innovations in methods like ultrasound-assisted processes are further enhancing recycling efficiency.
Part One: What are Lithium-ion Batteries?
Lithium-ion batteries (LIBs) have become a central technology in energy storage since their commercialization in the 1990s by Sony.
A lithium-ion cell consists of six main components that must all be recovered during the recycling process (see Figure 1). The anode and cathode are electrochemically active materials, while the separator electrically isolates the two electrodes.
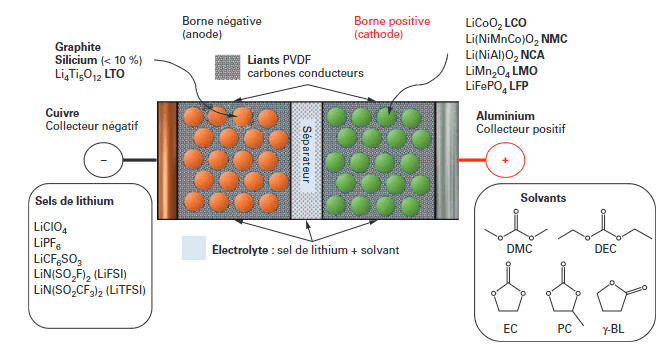
The negative electrode is typically made of lithium graphite (LixC6), though some technologies use lithium titanate (Li4Ti5O12) for enhanced safety, albeit at a higher cost and lower energy density. There is also a growing trend of replacing graphite with silicon, which can store more lithium ions, offering a higher mass capacity (2,200 mAh/g vs. 370 mAh/g for graphite). However, silicon electrodes face challenges with mechanical stress during cycling, limiting their long-term durability.
Lithium-ion batteries mainly differ by the chemistry of the positive electrode material. Three major classes of cathode materials can be distinguished:
- 1. Two-Dimensional Compounds: The first example is LiCoO2 (LCO), introduced by Sony in 1991, which offers high capacity and energy density. The nickel cobalt aluminum (NCA) compound (LiNi0.8Co0.15Al0.05O2) shares similar properties but is more affordable. Nickel manganese cobalt (NMC) compounds have also gained prominence since around 2010.
- 2. Three-Dimensional LiMn2O4 (LMO): This product is inexpensive and robust due to its three-dimensional structure, making it safe; however, it degrades poorly over cycling as manganese dissolves into the electrolyte.
- 3. Polyanionic LiFePO4 (LFP): This material uses the iron redox couple (Fe2+/Fe3+), with a potential of 3.5 V compared to 4.2 V for two-dimensional compounds and LMO (source).
Technological Developments
Battery specialists have defined generations of technology that have succeeded each other continuously since Sony's first LCO battery in 1991:
- Generation I (before 2010): LCO cathodes – graphite anode.
- Generation II (2010-2020): NCA/NMC 111 cathodes – graphite anode.
- Generation III (2020-): Low-cobalt cathodes (NMC622-NMC811) – silicon-enriched anodes.
- Generation IV (2030?): All-solid lithium metal batteries – cobalt-free oxides.
Recycling used batteries not only aims to reduce environmental impact but also focuses on recovering valuable components from electronic waste.
By 2040, it's estimated that recycling could provide 51% of the cobalt, 42% of the nickel, and 23% of the manganese used in battery production within the European Union. However, only 9% of lithium is expected to come from secondary sources.
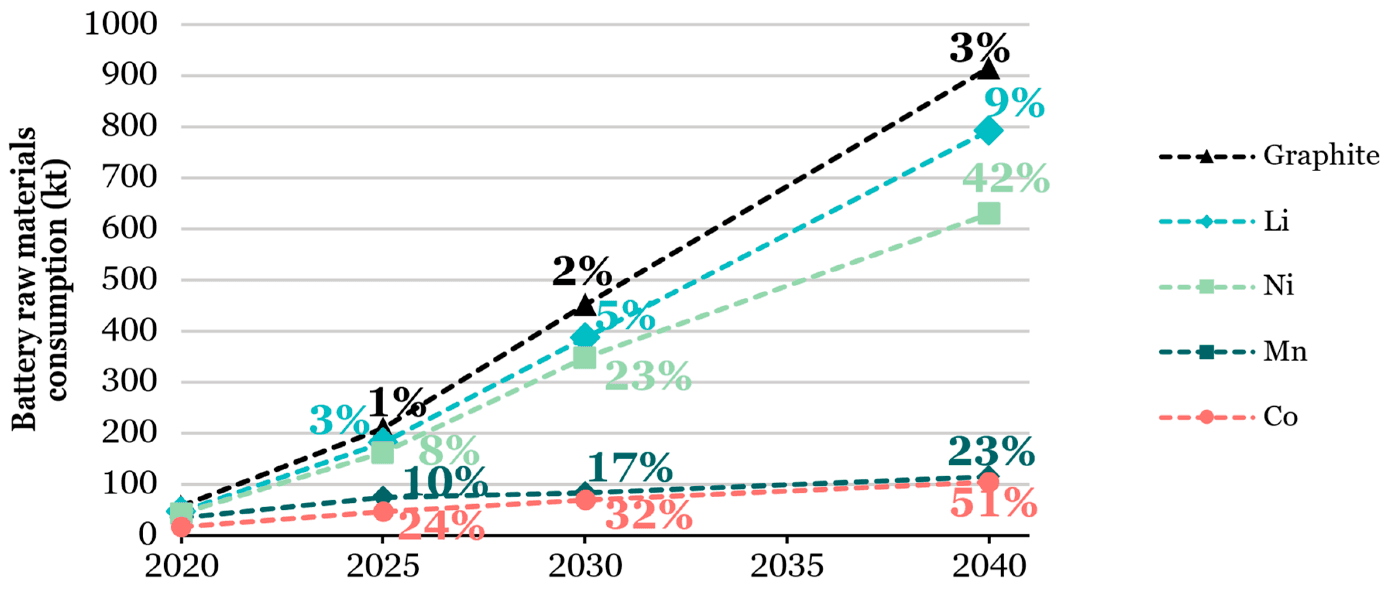
In response to the increase in LIBs production and the challenge of managing end-of-life batteries, several recycling technologies have been developed.
The three main approaches are pyrometallurgy, hydrometallurgy, and direct recycling:
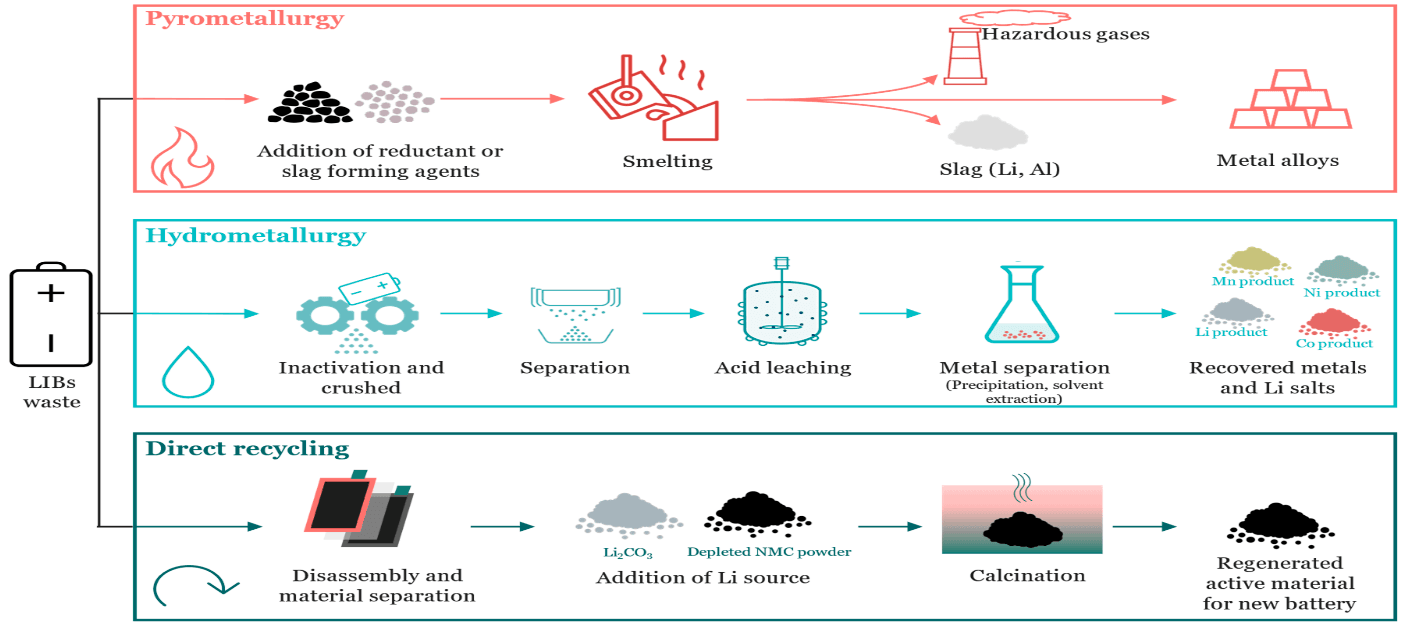
—1. Pyrometallurgy involves heating batteries to very high temperatures (up to 1,500°C) to melt and can separate heavy metals like cobalt, copper, and nickel (source). A few important aspects of this technology include:
- Quality of Recovered Materials: Metals may need additional treatment to achieve technical quality, particularly for iron and manganese.
- Environmental Impact: It is extremely energy-intensive, leading to high greenhouse gas emissions, and can produce toxic residues from the combustion of certain components. Additionally, lithium is often lost in the slags generated during the process.
- Challenges: The limited efficiency in recovering lithium diminishes its long-term sustainability appeal.
- Advantages: Widely used in industrial smelters due to its robustness and ability to handle heterogeneous batches of batteries without requiring prior sorting. Low operational costs due to the absence of sorting or mechanical pre-treatment requirements.
—2. Direct Recycling differs from the other approaches by attempting to reuse the active components of batteries, such as electrodes, without chemically decomposing them.
- Recovered Materials: Nearly all battery components, including active materials from both cathodes and anodes.
- Quality of Recovered Materials: May not perform as well as virgin materials; product quality can be affected by the mixing of different active materials.
- Environmental Impact: Direct recycling is the most environmentally friendly method, producing minimal waste and consuming less energy, resulting in a limited ecological impact.
- Challenges: Its development is hindered by the diversity of lithium-ion battery compositions and the lack of standardization, making it less effective for heavily degraded or contaminated batteries. Currently high cost due to the need for advanced processes; not yet viable on an industrial scale.
- Advantages: Involves mild thermal treatments or partial material replacements to restore cell performance. As newer generations of batteries become more homogeneous, the potential for this method is significant.
—3. Hydrometallurgy relies on the use of acid baths or chemical solutions to dissolve metals from spent batteries and recover them as purified salts.
- Recovered Metals: Cobalt, nickel, manganese, copper, lithium, and aluminum.
- Quality of Recovered Materials: High purity levels are achievable, suitable for battery-grade materials, though lithium recovery quality at a commercial scale is still being validated.
- Environmental Impact: Consumes less energy and produces no direct atmospheric emissions. However, it generates significant effluents that require treatment, and the use of toxic acids raises concerns about waste management.
- Challenges: Sorting batteries before processing is necessary, adding logistical complexity.
- Advantages: It is particularly effective in extracting valuable metals like lithium, cobalt, and nickel, accounting for 80.2% of the lithium-ion battery recycling market in 2022. Efforts are underway to develop more eco-friendly solvents to further minimize its environmental footprint.
Lithium-ion Battery Recycling Via Hydrometallurgy
Hydrometallurgical technology uses acidic solutions to extract valuable metals like lithium, cobalt, and nickel when recycling LIBs. The process involves grinding used batteries and dissolving metals with acids (e.g., H₂SO₄ or HCl) and reducing agents, enabling high-purity recovery and better selectivity compared to thermal methods.
In terms of innovation, efforts are focused on developing "Hydro 4.0," a concept aimed at making processes more environmentally friendly and automated by integrating advanced technologies such as data analytics and machine learning.
- Innovations
Companies and research institutions are investing in patented hydrometallurgical recycling technologies capable of processing various battery chemistries (LFP, NMC, LCO, etc.), thereby ensuring process flexibility.
- 1. Integration of Electrodialysis: Researchers at the University of Malaga have proposed using electrodialysis in hydrometallurgical recycling processes. This approach aims to improve the separation and recovery of valuable metals from spent batteries. It aligns with a circular economy logic by optimizing resource recovery while reducing environmental impact. However, challenges remain, particularly regarding energy consumption and system optimization.
- 2. Selective Leaching Technologies: Innovations in selective leaching aim to maximize metal extraction while reducing the use of reagents and waste production. These processes target critical metals with high efficiency and seek to make recycling both economically viable and sustainable. The challenge is to reconcile economic performance with reduced environmental impact by optimizing the chemistry used and the reaction conditions.
- 3. Hydrometallurgical Recycling via Biodegradable Acid Leaching: This innovation employs a mixed leaching system using biodegradable acids, including ascorbic acid and citric acid, to extract metals from spent batteries. Proposed by Fatima et al. (2024) through use of non-toxic and environmentally responsible reagents.
Each of these three recycling technologies plays a vital role in managing lithium-ion batteries sustainably. Pyrometallurgy is effective for large-scale processing but has a high ecological footprint. Direct recycling could further reduce environmental impact, especially as battery standardization improves. Future hybrid processes, along with stricter regulations, will likely drive innovation and support a circular economy as demand for batteries continues to grow. Hydrometallurgy offers a balanced approach with better efficiency and sustainability, making it the most promising method for EV batteries, though it requires careful chemical waste management. This is why the following patent landscape analysis focuses on this technology.
Part Two: Results of Our Battery Recycling Patent Analysis
Patent landscape analysis offers valuable insight into innovation, including helping us to predict the future of technology. In this part, we will share what our patent landscape analysis of innovation in hydrometallurgical lithium-ion battery recycling can tell us about the next generation of this technology, including the major industry players and main research and development (R&D) markets behind this innovative solution.
To understand the innovation and R&D activities in this technology, we performed a macro search using our proprietary IP intelligence software. By analyzing the patents collected using our IP Consulting services expertise, we were able to create a fascinating global insight into research advancement and investment in this field.
In total, the database comprises 2,958 patent families filed in the last 20 years. Patent filing dynamics reveal a significant rise in patent activity related to hydrometallurgical Li-ion battery recycling from 2004 to 2024, with a sharp increase starting from 2017.
Early years exhibit relatively low patent filings, however, starting from 2017, there has been a significant surge. By 2020, the number of granted patents peaked at 190, marking a 144% increase from the 78 patents granted in 2017. Similarly, the number of pending patents increased substantially from just 4 in 2017 to 127 in 2021, reflecting an exponential growth (as shown below).
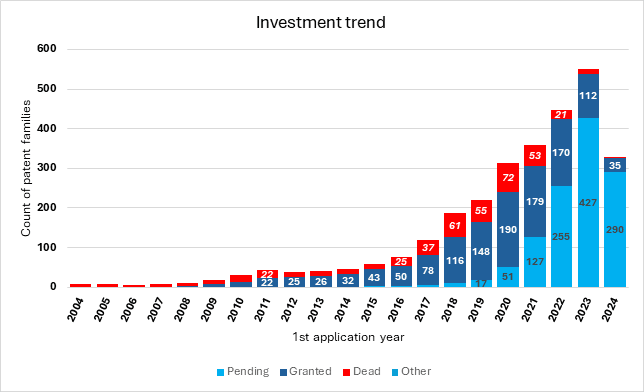
This surge is driven by rising demand in electric vehicles, consumer electronics, and energy storage, along with an emphasis on sustainable recycling to manage battery waste and recover materials essentially lithium, cobalt, and nickel for the green transition.
Key Trends: Filing Periods
- 2004-2008: The period shows minimal patent activity, with only a few dead patents, indicating that the field was still in its early development stages and that demand for electrical energy storage technologies was relatively low compared to recent trends.
- 2009-2015: The number of granted patents begins to rise slowly and steadily, reflecting gradual technological advancements and the growing demand for efficient battery recycling solutions.
- 2016-2021: The number of granted patents shows a sharp increase, indicating high approval rates, while pending patents also rise moderately. This trend likely reflects the EU’s 2020 proposal under the European Green Deal to replace the 2006 Battery Directive with ambitious recycling and recovery targets, along with a new battery passport. Similarly, China’s 2018 Interim Measures establish robust battery traceability and recycling standards, promoting comprehensive lifecycle management and advancements in battery design and second-life applications (source).
- Incomplete years that demonstrate high figures, particularly for pending patents, highlighting interest and innovation in the field, driven by ambitious regulatory goals, including the EU's targets for 70% portable battery collection by 2030 and 95% recovery of materials like cobalt and lithium, alongside China's mandates for 50% recycling of lithium-ion batteries by 2025 and 98% recovery targets for nickel, cobalt, and manganese.
Top Players for Hydrometallurgical Li-ion Battery Recycling
Our patent landscape analysis reveals the key players in the hydrometallurgical recycling of Li-ion batteries field.
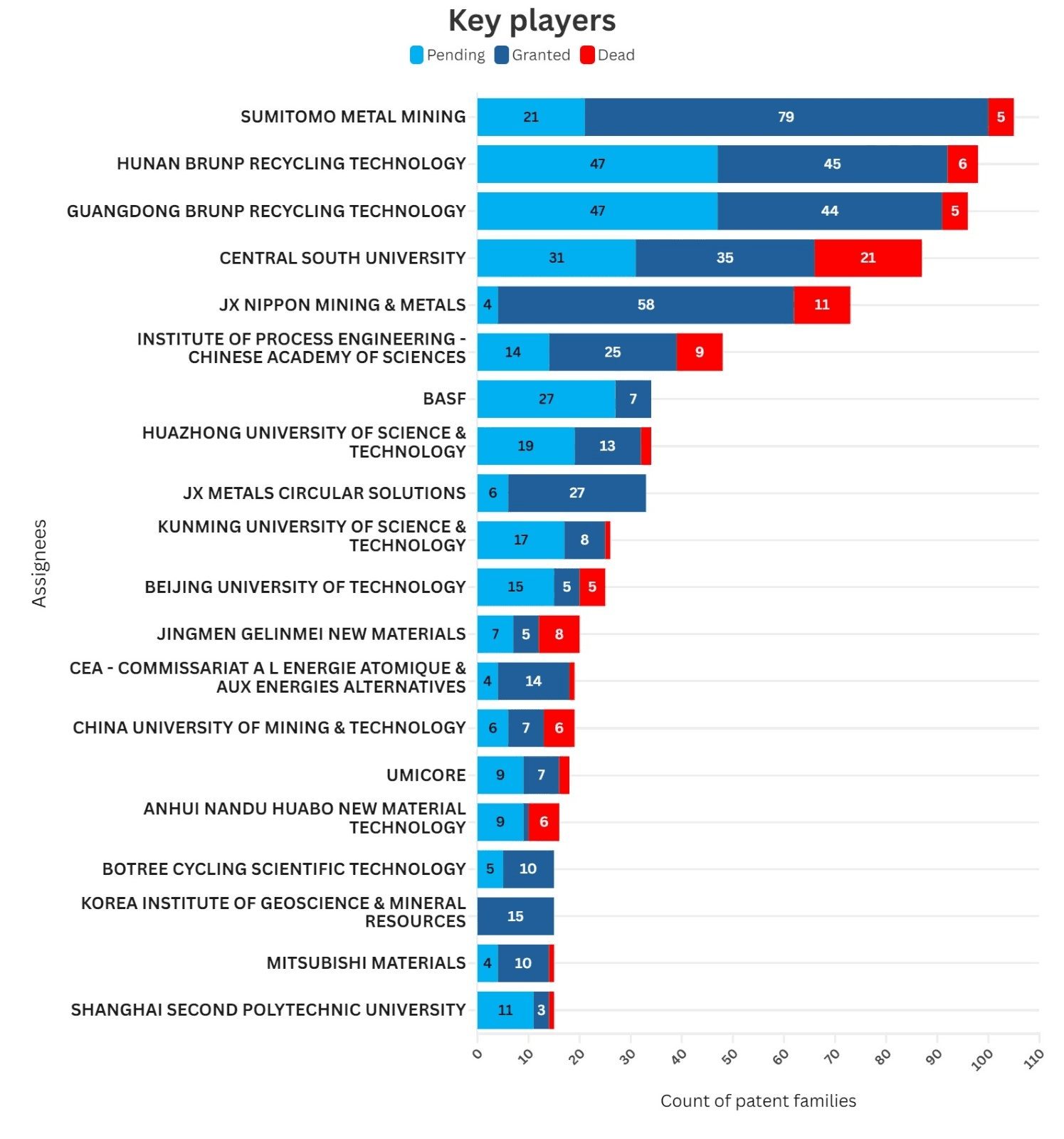
- Sumitomo Metal Mining Co. Ltd., a leading Japanese mining and smelting company, holds 79 granted patents and 21 pending patents, reflecting a robust intellectual property portfolio in the field. The company has made significant strides in hydrometallurgical recycling of LIBs focusing on environmentally friendly processes to efficiently recover valuable metals like lithium, cobalt, and nickel. Its innovations, including enhanced solvent extraction methods, aim to improve metal recovery effectiveness while minimizing environmental impact, promoting a sustainable approach to battery recycling.
- Hunan Brunp Recycling Technology and Guangdong Brunp Recycling technology, both subsidiaries of the leading Chinese battery manufacturer CATL (Contemporary Amperex Technology Co., Ltd.), specialize in the recycling of LIBs. Hunan Brunp focuses on dismantling and hydrometallurgical processing of spent batteries, while Guangdong Brunp concentrates on recovering key metals. With 45 and 44 granted patents, respectively, along with 47 pending patents, these companies are advancing recycling technologies and reinforcing China’s commitment to leadership in the circular economy for LIBs. The limited number of expired patents suggests that their innovations remain highly relevant and at the forefront of the rapidly evolving battery recycling sector.
- Central South University and Institute of Process Engineering, Chinese Academy of Sciences are leading academic institutions contributing significantly with 35 granted patents, and 31 pending patents for Central South University and 25 granted patents for the Institute of Process Engineering. Their contribution underscores the importance of research institutions in innovating sustainable recycling technologies, particularly in China.
- BASF is one of the largest chemical companies in the world, with 27 pending and 7 granted patents, it represents a significant European player. Collaborating with industry leaders like Iveco Group and Stena Recycling, BASF advances electric vehicle battery recycling processes, prioritizing resource efficiency and sustainability. Meanwhile, its North American partnership with Nanotech Energy focuses on reducing CO₂ emissions by producing lithium-ion batteries that incorporate recycled materials. Through ongoing collaborations with academic institutions, BASF continues to drive innovation in battery materials, reinforcing its commitment to sustainable solutions in energy storage.
- JX Nippon Mining & Metals (58 granted patents, 4 pending patents, and 11 expired patents) alongside its recycling-focused subsidiary JX Metals Circular Solutions (27 granted patents) showcases Japan’s technological leadership in advanced metal recovery and recycling from lithium-ion batteries. These innovations, strengthened by a partnership with Mitsubishi Materials, which holds 10 granted patents, provide closed-loop recycling solutions for electronic and automotive waste, aiming to secure a stable supply of recycled materials while supporting Japan’s commitment to a circular economy and global decarbonization goals in the battery and electronics industries.
- Commissariat à l'Énergie Atomique et aux Énergies Alternatives (CEA) holds a moderate portfolio of 14 granted patents and 4 pending patents. This focus aligns with its mission as a French public research organization to advance sustainable technologies and contribute to France’s circular economy goals. For lithium-ion batteries, CEA emphasizes the treatment and recycling of lithium, cobalt, manganese, and nickel.
Hotspots for Hydrometallurgical Technology Lithium-Ion Battery Recycling Technologies
Priority country filing most often occurs in the country in which the research and development (R&D) takes place, so looking at this data shows us which countries are the most innovative and which are the ones that seek to protect their inventions.
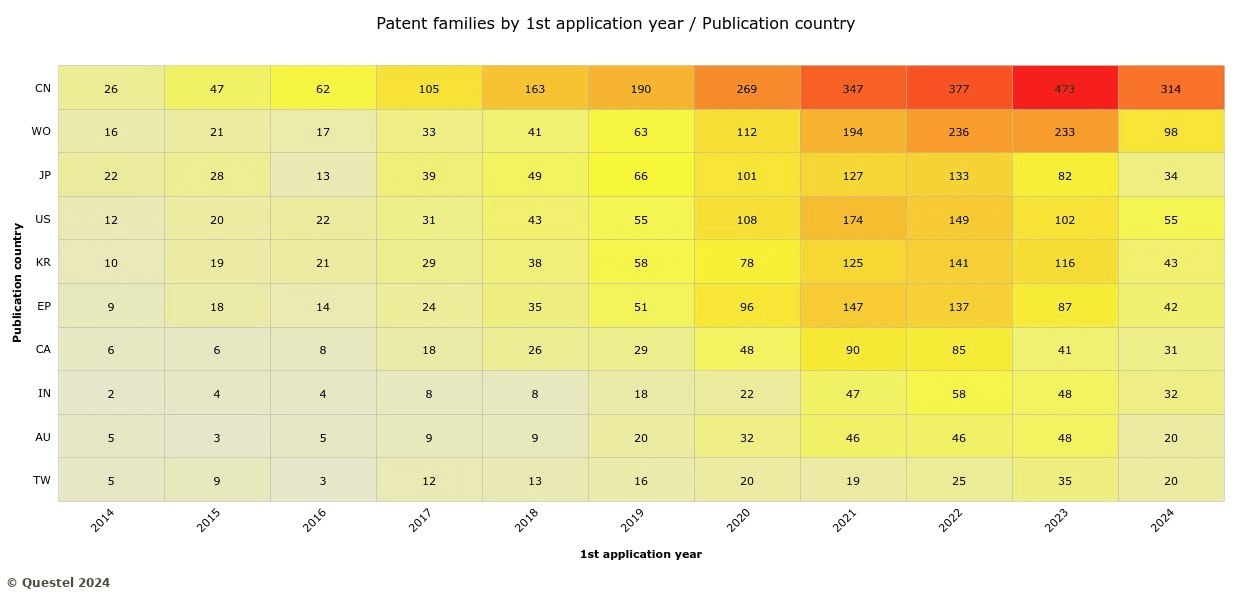
The geographic distribution of patents in hydrometallurgical technology for recycling lithium-ion batteries reveals that the majority of activity is concentrated in China.
- China (CN) shows a significant increase in patent applications over the years, particularly from 2016 onwards, already reaching a peak of 473 patent families in 2023 even though the year might be incomplete. This trend highlights China’s strong focus on LIBs recycling, driven by its extensive battery production and consumption. Such leadership in patent filings reflects China's dominance in the global battery supply chain and its growing focus on recycling technologies.
- Japan (JP) has a steady increase in patent filings, peaking between 2018 and 2021. This trend reflects Japan’s focus on securing resources like lithium and cobalt through recycling, given its limited domestic supply. Japan’s commitment to innovation in recycling technologies aligns with its strategic goals for resource security and environmental sustainability.
- World Organization (WO) patent applications show a gradual increase, peaking around 2020-2023. This trend indicates a growing international interest and active innovation in this field.
- United States (U.S.), South Korea (KR), and Europe (EP) exhibit moderate but steady growth in patent filings, highlighting their roles in the global battery recycling industry. The U.S. and South Korea show consistent filings, peaking around 2020-2022. The heatmap indicates an upward trend in filings since 2010, with rapid growth from 2018-2022, driven by rising demand for LIB in electric vehicles, electronics, and renewable energy, along with the need for sustainable disposal solutions.
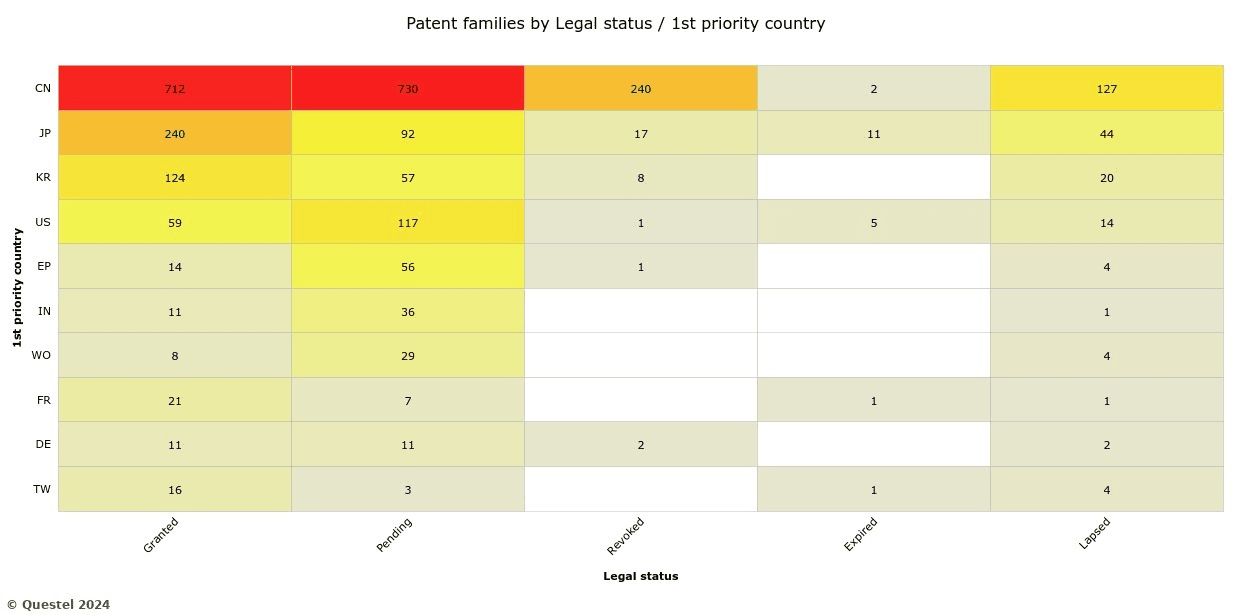
- China leads significantly with over 1,800 patent families, of which 712 are granted and 730 are pending, showcasing the country’s dominance and commitment to this field.
This aligns with China’s push for sustainability, reflected in the production of 9.3 million EVs in 2023 (65% of global production) and the sale of 8.4 million units, 59% of global sales, with approximately 90% of those sales being domestic in 2023 (source). The scale of EV production and consumption establishes China as a primary market for LIB recycling, driving advancements in eco-friendly and efficient metal recovery methods.
- Japan demonstrates strong activity with 240 granted patents and 92 pending applications. Japan’s commitment to innovation in LIB recycling is evident, signaling a robust pipeline of advancements in sustainable battery management.
- The United States (U.S.) shows a proactive approach, with 59 granted patents and 117 pending patents, U.S. efforts focus on refining recycling processes, exploring novel methods like deep eutectic solvents for metal extraction, and developing scalable solutions to address growing battery waste. One such innovation is Aqua Metals’ patent-protected AquaRefining™ process, which was initially applied to lead recycling and is now being extended to lithium-ion battery processing. This method, which utilizes water at ambient temperature, reduces pollutant emissions and enables efficient recovery of metals. However, despite its environmental benefits, large-scale commercialization of this patent-protected technology remains a challenge.
- South Korea (KR) presents a considerable patent activity, with 124 granted patents and 57 pending patents, reflecting a strategic focus on resource recovery and green technology. Government-supported R&D and academic-industry collaborations aim to enhance recycling efficiency and reduce reliance on imported raw materials.
- Europe (EP), with 14 granted patents and 56 pending patents, has shown a marked increase in patent activity for hydrometallurgical technology for battery recycling. This trend aligns with EU policies promoting sustainable technology and reducing electronic waste, making hydrometallurgical recycling a priority for both environmental and economic reasons across Europe.
- Other countries, like India, show smaller numbers of patents, likely indicating emerging or more niche interest in this field.
What Patent Analysis Reveals About the Future of Battery Recycling
Hydrometallurgical technology for battery recycling offers a promising path forward in the sustainable management of lithium-ion batteries. By using chemical processes to recover valuable metals like lithium, cobalt, and nickel, this approach can efficiently reclaim high-purity materials, which is crucial for meeting the growing demand driven by electric vehicles, consumer electronics, and renewable energy storage systems.
The surge in patent activity related to hydrometallurgical recycling highlights the increasing global focus on developing innovative and cost-effective solutions. Countries like China and Japan are leading the way, driven by ambitious regulations and strategic goals to secure essential raw materials through recycling. Major industry players and research institutions are actively exploring new techniques, such as selective leaching and the integration of advanced technologies, to improve efficiency and reduce environmental impact.
Recent trends also show growing interest in collaborative efforts between industry and academia, emphasizing the importance of continued innovation to address the challenges of battery waste. With advances in automation and eco-friendly processes, the future of battery recycling appears bright. As regulatory frameworks strengthen globally, supporting circular economy principles, hydrometallurgical recycling will likely play a critical role in reducing our dependence on mining and creating a more sustainable energy landscape.
Patent landscape analysis can provide valuable insights into research and innovation trends and markets, as we hope this analysis of hydrometallurgical LIBs recycling illustrates. For further details on patent activity in this sector or for specific advice or support on any other topic, contact the Questel IP Consulting team.
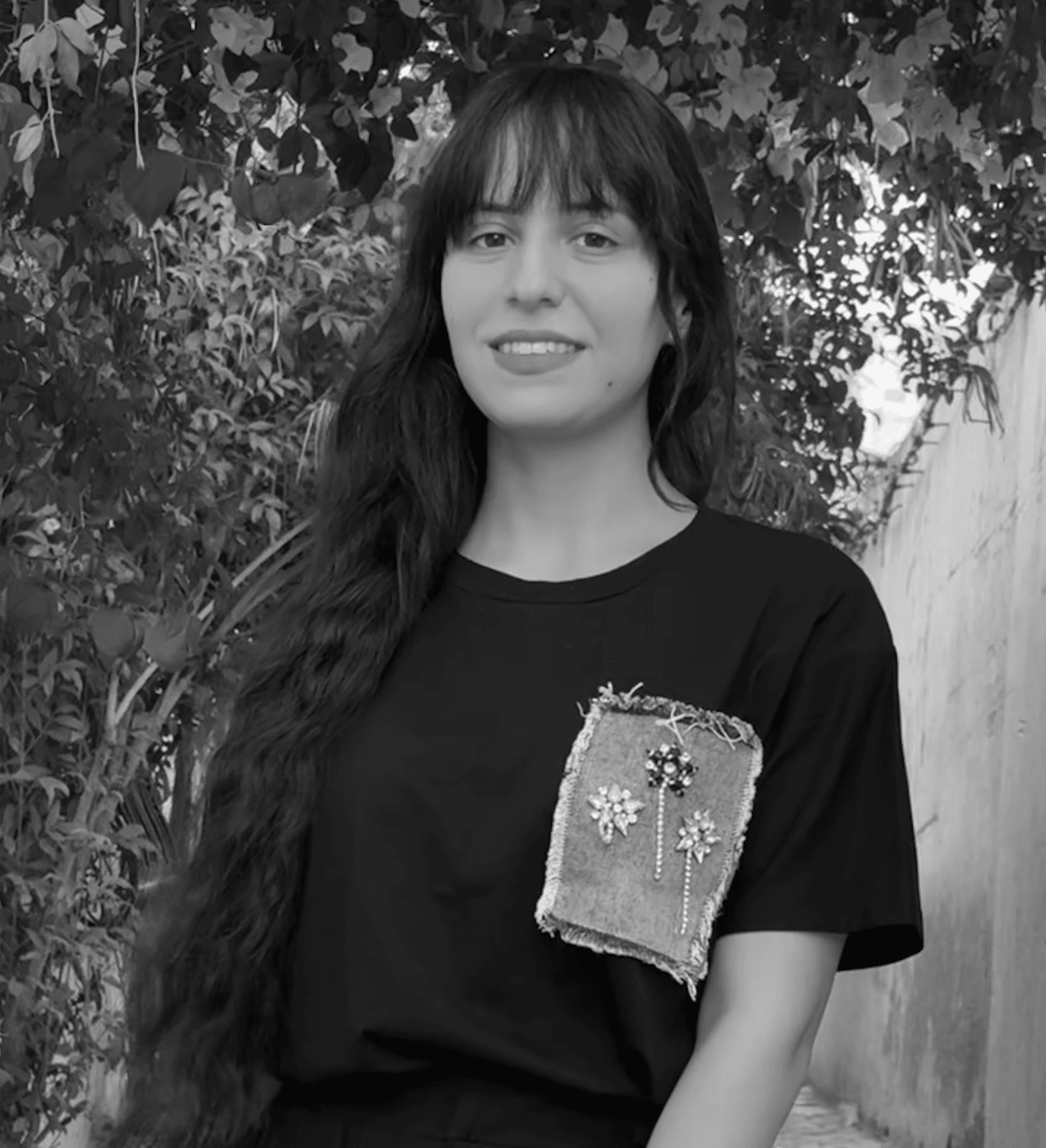